Mastering Precision Injection Molding: Unveiling the Art of Manufacturing Excellence
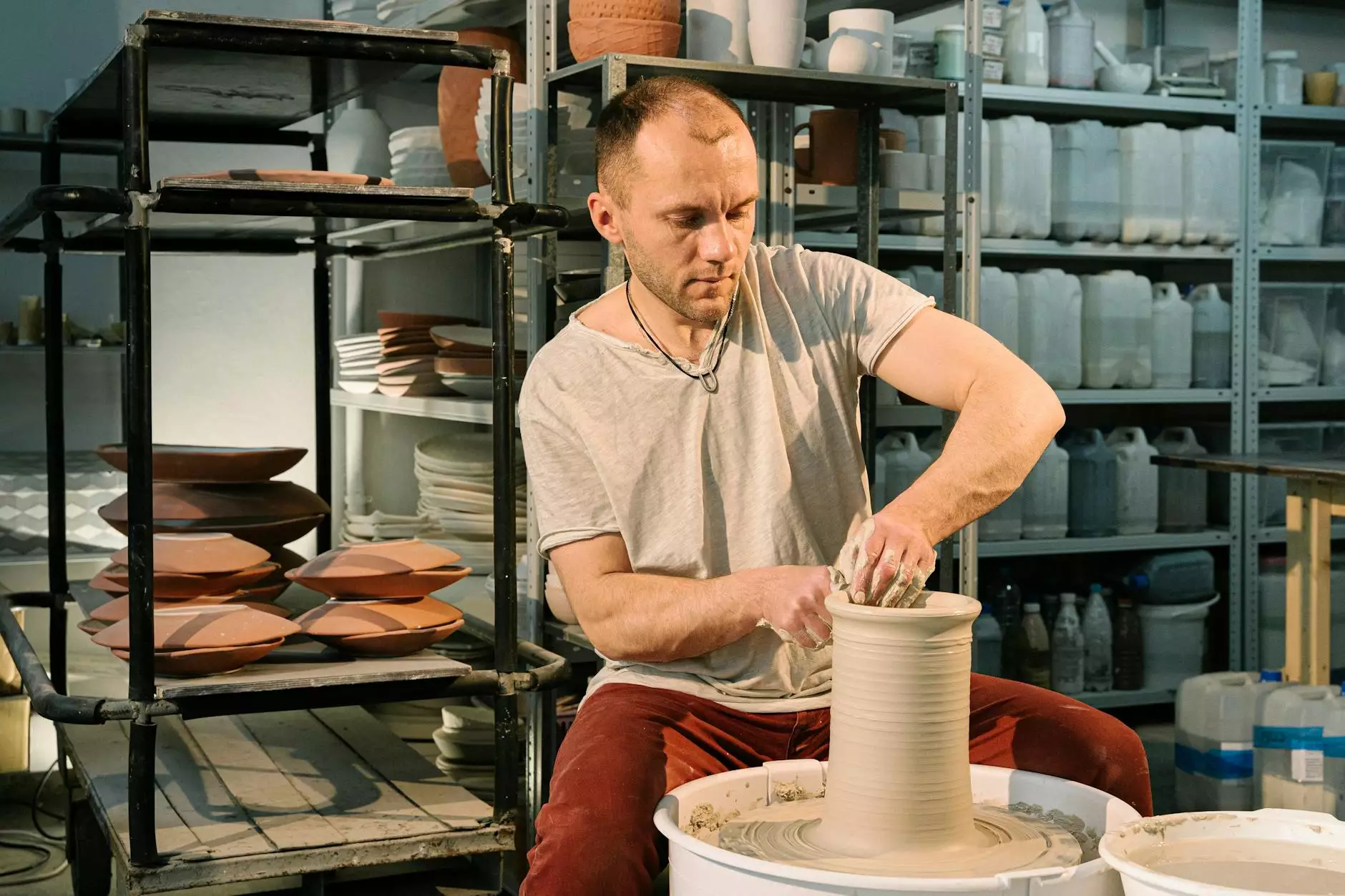
In today's highly competitive industrial landscape, the demand for precision and efficiency in manufacturing processes is ever-growing. Among the various methods employed in modern manufacturing, precision injection molding stands out as a remarkably effective solution. As a premier precision injection molding manufacturer, Deep Mould specializes in delivering top-tier products that not only meet but exceed client expectations. This comprehensive article aims to explore the intricacies of precision injection molding, its advantages, the technology behind it, and its pivotal role in various industries.
Understanding Precision Injection Molding
At its core, precision injection molding is a method of manufacturing by which molten material, typically plastic, is injected into a mold under controlled pressure and temperature conditions. This process allows for the creation of highly detailed and complex parts with exceptional repeatability and high dimensional accuracy.
The Process of Injection Molding
The injection molding process consists of several crucial steps:
- Material Selection: The choice of the material is essential. Common materials used include thermoplastics, thermosetting plastics, and elastomers, each offering unique properties tailored to specific applications.
- Mold Design: Designing a mold that meets the desired specifications and tolerances is fundamental to achieving high-quality outcomes. This stage often involves advanced computer-aided design (CAD) technologies.
- Injection: The selected material is heated until it becomes molten and is then injected into the mold under high pressure, ensuring that it fills every cavity, even the most complex ones.
- Cooling: Once the mold is filled, it is cooled to solidify the material, enabling it to retain the shape of the mold.
- Demolding: After sufficient cooling, the mold opens to release the finished part, which may require further finishing operations depending on its intended use.
Benefits of Precision Injection Molding
The advantages of leveraging precision injection molding for manufacturing are manifold:
- High Efficiency: Once the mold is created, parts can be produced rapidly, significantly reducing cycle times and enhancing overall productivity.
- Cost-Effectiveness: Although the initial setup for molds may involve significant investment, the long-term production of parts at a low cost per unit becomes highly advantageous, especially for high-volume production runs.
- Unmatched Precision: With advanced control systems and high-quality molds, the dimensional accuracy and surface finish of the products are exceptional, making it ideal for industries requiring stringent tolerances.
- Material Versatility: Precision injection molding can accommodate a wide variety of materials, allowing manufacturers to select the best material for their specific applications.
- Complex Geometries: The ability to create intricate designs and geometrical features is unparalleled, enabling innovative product development.
The Role of Technology in Precision Injection Molding
Advancements in technology have propelled precision injection molding into new frontiers. Sophisticated software such as computer-aided manufacturing (CAM) and various simulation tools allow manufacturers to optimize the injection molding process before actual production begins.
Modern machines are equipped with advanced temperature control, pressure monitoring, and automated features that enhance efficiency and reduce the likelihood of defects. Automation in the injection molding process not only reduces labor costs but also improves consistency, making sure each part produced meets the preset quality standards.
Integrating Industry 4.0
The emergence of Industry 4.0 has transformed the landscape of manufacturing, including precision injection molding. Smart factories leverage the Internet of Things (IoT), big data analytics, and cloud computing to monitor and control the injection molding processes in real-time, resulting in:
- Improved Predictive Maintenance: Monitoring equipment performance helps to anticipate and prevent breakdowns before they occur.
- Enhanced Quality Control: Utilizing real-time data analytics can alert manufacturers to potential quality issues immediately, enabling quick corrective actions.
- Increased Customization: Industry 4.0 allows for greater flexibility, enabling manufacturers to adapt and customize products based on client specifications more rapidly.
Applications of Precision Injection Molding
The versatility of precision injection molding makes it suitable for an extensive range of applications across numerous industries, including:
Automotive Industry
The automotive sector benefits immensely from precision injection molding, where lightweight and durable plastic components are critical for vehicle performance and fuel efficiency. From dashboards to exterior panels, precision-molded parts are integral to modern vehicle design.
Medical Devices
The medical industry has stringent quality and regulatory demands. Precision injection molding brings a high level of reliability to the manufacturing of components such as syringes, catheters, and implants, ensuring they meet the necessary safety standards.
Consumer Goods
From household appliances to electronic devices, precision injection molding allows for the efficient production of aesthetically pleasing and functional consumer products. The ability to create complex designs enhances product appeal and competitiveness in the market.
Electronics
In the electronics industry, precision parts such as housings, connectors, and protective casings must meet rigorous specifications. Injection molding achieves the required dimensional accuracy and surface finish crucial for electronic applications.
Choosing the Right Precision Injection Molding Manufacturer
When searching for a precision injection molding manufacturer, consider the following factors:
- Experience and Expertise: An experienced manufacturer is likely to have a well-established process, understanding of materials, and the capability to deliver high-quality products.
- Technological Capabilities: Ensure the manufacturer employs advanced technologies that allow for precision molding, quality control, and adaptability to customer needs.
- Quality Assurance: Look for manufacturers that prioritize quality management systems and certifications to ensure adherence to industry standards.
- Customer Support: A reputable manufacturer provides strong customer support and communication throughout the production process, ensuring customer goals are met.
The Future of Precision Injection Molding
As industries continue to evolve, the future of precision injection molding appears bright. Innovations in materials, including biodegradable and recycled plastics, are leading the way towards more sustainable manufacturing practices. Moreover, the incorporation of artificial intelligence and machine learning will undoubtedly improve operational efficiencies and product quality.
In summary, precision injection molding plays a vital role in modern manufacturing, offering unparalleled efficiency, precision, and versatility across various industries. Partnering with a leading provider like Deep Mould ensures that your manufacturing needs are met with the highest standards of quality and innovation. As manufacturing technology continues to advance, keeping pace with these developments will allow businesses to reap the benefits of precision injection molding, enhancing their competitiveness in the global market.
Conclusion
In conclusion, precision injection molding is more than just a manufacturing process; it is a powerful tool that shapes industries and drives innovation. By understanding its fundamentals, benefits, and applications, businesses can leverage this technology to propel themselves toward success in an increasingly complex market. With trusted partners like Deep Mould by your side, the possibilities are limitless.