Understanding Manifold Valve Working: A Comprehensive Guide
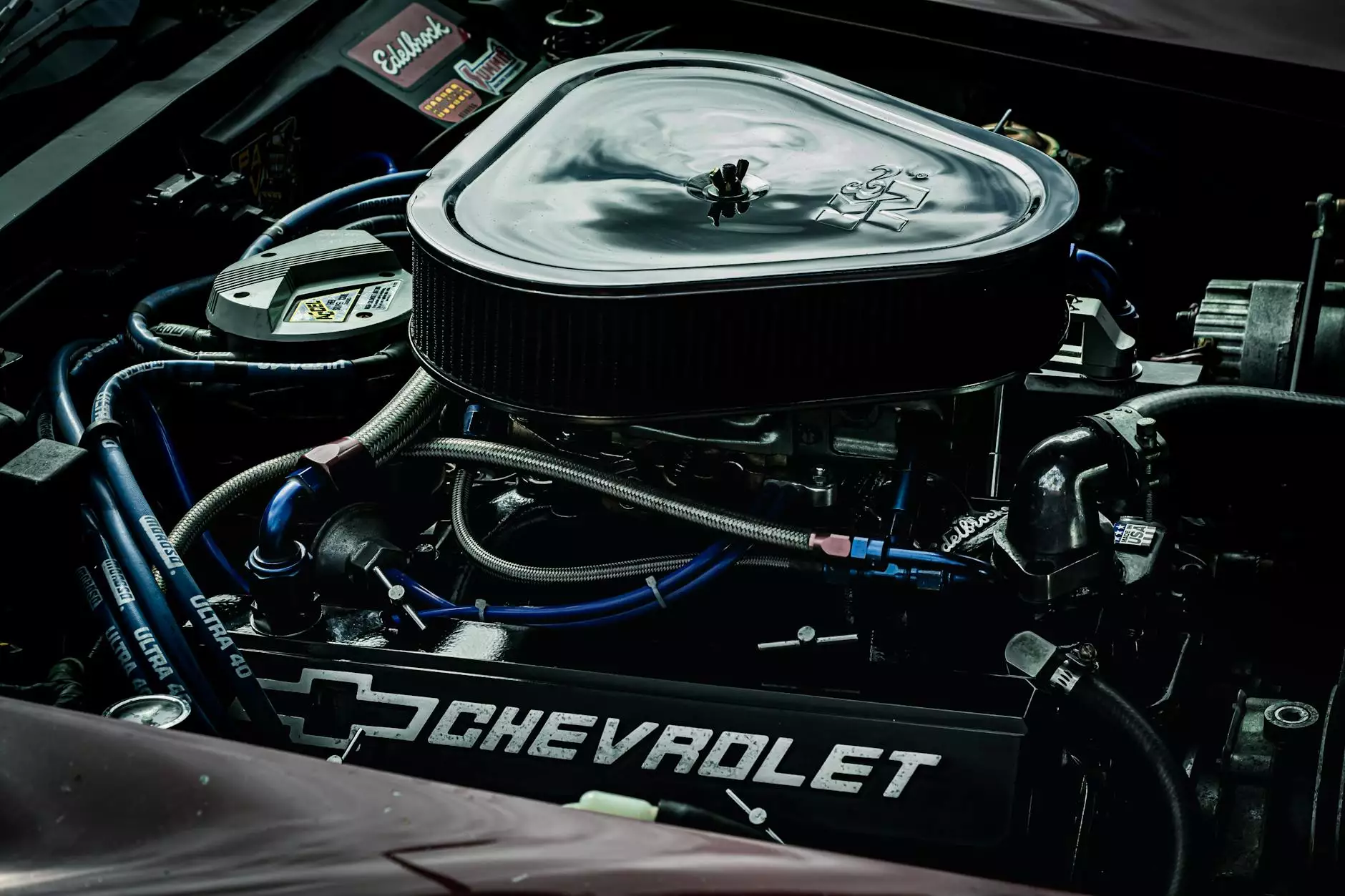
The world of fluid dynamics and control systems would be incomplete without a thorough understanding of manifold valves. In this detailed guide, we will explore manifold valve working, their design, applications, and significance in various industrial sectors. As a key component in hydraulic and pneumatic systems, mastering this subject can greatly enhance operational efficiencies across numerous applications.
What is a Manifold Valve?
A manifold valve serves as a junction point in a hydraulic or pneumatic system, allowing for the right control and flow of fluids. Essentially, it consolidates various controlling valves, gauges, and other accessories into a single body, significantly simplifying the layout of piping systems. By streamlining connections and functions, manifold valves facilitate easier maintenance and enhanced functionality.
How Does a Manifold Valve Work?
To understand manifold valve working, one must consider its key components and their functionalities:
- Inlet Ports: These are the points through which fluid enters the manifold.
- Outlet Ports: These facilitate the flow of the fluid out of the manifold to various applications.
- Control Mechanism: This can vary from manual levers to automated electronic controls, enabling operators to manipulate fluid flow as needed.
- Seals and Gaskets: Essential for preventing leaks and maintaining pressure within the system.
The functioning of a manifold valve can be summarized in the following steps:
- The *operator* actuates the control mechanism, which either opens or closes the valve.
- Fluid enters through the inlet ports.
- The manifold directs the fluid to the outlet ports, allowing for distribution to various circuits.
- Exit pressure and flow rates can be monitored and adjusted as needed.
Types of Manifold Valves
There are several types of manifold valves, each designed for specific applications:
- 4-Valve Manifold: Commonly used in pressure measurement applications, providing clear pathways for measurement and control.
- 3-Valve Manifold: Typically used in regions where fluid mixture and separation are vital.
- 2-Valve Manifold: Best suited for simpler systems requiring less control complexity.
Applications of Manifold Valves
Manifold valves find widespread use across multiple industries, including:
- Oil and Gas: They control pressure and streamline the workflow in drilling and extraction processes.
- Aerospace: Utilized in hydraulic systems, where precision is vital for safety and performance.
- Manufacturing: Employed in production lines where control over fluid dynamics is required.
- Automotive: Integral to the operation of various automotive systems including brakes and steering.
The Advantages of Using Manifold Valves
Choosing to implement manifold valves in your operations brings numerous advantages:
- Space-saving Design: Consolidating multiple components into one unit reduces the overall space required.
- Improved Safety: With fewer connections to monitor, the risk of leaks and accidents decreases.
- Enhanced Operational Efficiency: Simplified control leads to faster response times and greater accuracy.
- Easy Maintenance: Having all valves in one location makes for quicker inspections and repairs.
Key Considerations When Selecting a Manifold Valve
When choosing the right manifold valve for a specific application, several critical factors should be taken into account:
- Material Compatibility: Ensure that the valve materials are suitable for the fluids being handled.
- Pressure Ratings: The manifold must withstand the maximum operating pressure required for the application.
- Flow Rate Requirements: Determining the appropriate size to manage the expected flow rates efficiently.
- Maintenance Considerations: Assess how easy it will be to maintain and service the valve in its operating environment.
Common Issues with Manifold Valves and How to Fix Them
Even the most well-designed manifold valves can encounter issues. Here are some common problems along with solutions:
- Leaking Seals: Inspect seals regularly and replace them as needed to prevent leaks.
- Blocked Ports: Ensure that the inlet and outlet ports are free of debris and build-up.
- Control Failures: Conduct periodic checks on the actuator mechanisms to ensure they are functioning correctly.
Future Trends in Manifold Valve Technology
The demand for more efficient and sturdier valves is driving innovation in manifold valve technology. Future trends may include:
- Smart Valves: Automated systems that utilize IoT for real-time monitoring and control.
- Sustainability: Development of environmentally friendly materials and design processes.
- Advanced Materials: Introducing stronger, lighter materials to improve durability.
Conclusion
Understanding manifold valve working is crucial for professionals in various sectors dealing with fluid dynamics and control. The manifold valve not only simplifies complex systems but enhances operational efficiency and safety. Whether you are in the oil and gas industry, aerospace, manufacturing, or automotive sectors, a solid grasp of manifold valves can significantly impact your operation's effectiveness. Keep abreast of technological advancements, and ensure your processes are optimized for performance and sustainability.